The increased public awareness of the health, environment and safety concerns associated with the use of some organic solvents in food processing and the possible solvent contamination of the final products. The high cost of organic solvents and the increasingly stringent environmental regulations together with the new requirements of the medical and food industries for ultra-pure and high added value products have pointed out the need for the development of new and clean technologies for the processing of food ingredients.
Supercritical fluid extraction, using carbon dioxide as a solvent, has provided an excellent alternative to the use of chemical solvents. Over the past three decades, supercritical CO2 has been used for the extraction and isolation of valuable compounds. It is non-toxic, leaves no residues, and is considered a green manufacturing process.
Supercritical fluid extraction process: unique and innovative extraction process
Supercritical fluid extraction (SCFE) process has emerged as the alternative to the traditional solvent extraction process. It is a separation technique, which is developed by use of the fluid that has the ability of dissolution at supercritical pressure and supercritical temperature.
The extraction is carried out in highpressure equipment in batch or continuous manner, the supercritical solvent is put in contact with the material from which a desirable product is to be separated. The supercritical solvent, now saturated with the extracted product, is expanded to atmospheric conditions and the solubilized product is recovered in the separation vessel permitting the recycle of the supercritical solvent for further use (Figure 1).
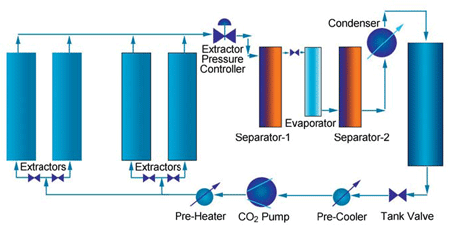
As the extractions are carried out at high pressures, the extraction unit is fully automated, computerized, and highly sophisticate. Communication interfaces and input/output modules match the most challenging requirements in industrial automation thereby creating high degree of consistency and reproducibility between batches/lots.
Characteristics of supercritical fluid extraction process
The supercritical fluid extraction technique has many characteristics:
-High extraction efficiencies;
- Simple separation technology;
- No need for solvent recovery equipment;
- Easy operation condition;
- Always completed at the room temperature and is carried out close to ambient temperature conditions. Supercritical Fluid Extraction using CO2 is today a popular technology for rapid, contamination-free extraction. CO2 is inert, safe, inexpensive, non-flammable and non-toxic solvent.
Industrial application of supercritical fluid extraction process
The special properties of supercritical fluids bring certain advantages to chemical separation processes. Several applications have been fully developed and commercialized.
Nutraceuticals
The Nutraceutical market is still a nascent market with potential for revenue in the coming years. In particular, the most interesting areas of Nutraceutical products are pointed in the products with effect in the immunological system, cancer risk, cardiovascular illness and elevated levels of cholesterol in the blood. SCFE provides interesting alternatives for development of Nutraceuticals. Its capacity can be considered as a strategic property. With SCFE technology it is feasible to remove solvent traces, aromas, flavors, fats etc.
Pharmaceuticals and Chemicals
Pharmaceutical industries as well as chemical industries are changing some of these traditional practices to accomplish fresh green goals. Thus extraction with carbon dioxide under supercritical conditions constitutes an emerging technology in terms of environmental impact.
Food and Flavoring- Extraction of natural spices
A very successful application of supercritical fluid extraction technique is the distillation of natural spices. Supercritical fluid extraction has the ability of high dissolution, high extraction yield and is efficient. CO2 is used as the extraction agent, the products are non toxic, leaves no residues, their color and fragrance are excellent. - Essential oils obtained from plant matrix form the basis of many pharmaceutical compounds in use nowadays and are the raw materials of flavors and fragrances. However, the traditional methods for extraction, such as hydro distillation, steam distillation, solvent extraction, and simultaneous distillation extraction are time consuming, labor intensive, and may violate new stringent environmental regulations. Thus supercritical fluid extraction is a viable alternative for many applications including essential oils extraction from herbs.
Natural products, especially essential oils that are aromatic liquids separated from herbal plants, represent the main raw materials for flavor, fragrances and pharmaceuticals. Flavoring and fragrance ingredients are the most numerous single group of international additives used by the food and personal care industries. Their market growth rate is increasing with time on an international level. The WHO regulations are changing to be strict, to safeguard the human health and a survey has been issued indicating that about 70-80% of the world populations rely on nonconventional medicine mainly of herbal sources in their primary health care. In time, traditional separation techniques such as hydro distillation, steam distillation, solvent extraction, and simultaneous distillation extraction need to be substituted by sustainable and green separation techniques.
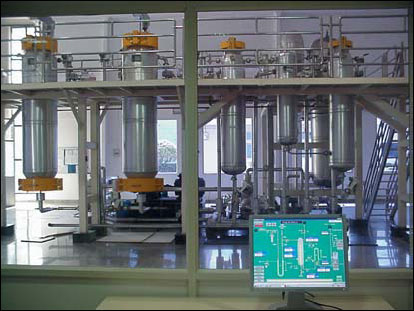
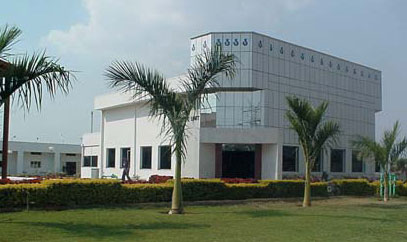
Main advantages
The SCFE extracts are regarded as very high quality as there are no chemical changes due to reactions or thermal degradation as the extractions are carried out using moderate processing temperatures.
- SCFE process is becoming increasingly popular due to its inherent potential for high recoverability and selectivity, fractionating superior-grade natural extracts from a variety of biomaterials.
- SCFE Process is an environmentally friendly process for industrial production. It meets safety regulations and legal restrictions as well as the increasing demand for the use of natural products.
- The Carbon Dioxide used in the SCFE process is non-toxic, odorless, tasteless, neutral, nonflammable and fully accepted as food grade solvent with GRAS status.
- High purity and tailor made specifications of the product due to easy manipulation and selectivity of separation.
- A wide spectrum of physical properties can be obtained in a single solvent by small variation of process parameters such as pressure and temperature.
- The SCFE extracts are known for accuracy, precision, specificity and linearity.
- Improved product consistency because of accurate controlled process parameters.
SCFE is the Technique of Choice for Many Important Nutraceuticals, Essential Oils and Spice Extracts
SCFE Process Ideal for
- Extraction of natural spices: Black Pepper, Celery Seed, Cumin, Cinnamon, Clove Bud, Nutmeg etc;
-Extraction of Natural Colors: Pigments from Paprika, etc;
- Extraction of actives from botanicals: Dry Ginger, Saw Palmetto, Rosemary etc;
- Extraction of Nutraceuticals, Cosmeceuticals:Forskolin, Turmerones - from Turmeric,Oscimum sanctum, Neem Leaf
-Extraction of cholesterol and other lipids from dried egg yolk;
-Extraction of Hops for the beverage industry;
- Biochemical components: Precipitation of Human Immunoglobulin G (IgG),
Inactivation of viruses etc.
Conclusion
Sustainability has also become a leading strategy for new successful product and process development for the 21st century. Therefore new industrial processes which offer ecological and social advantages are demanded. New processes using Supercritical fluids, which improve current ones in simplicity, energy saving, recycling and in quality of obtained products, constitute clean processes in the frame of environmentally accepted technologies. Supercritical Fluid Extraction is becoming increasingly important as an environmentally acceptable replacement for more traditional solvents in the move towards Green Chemistry.
References
1) Mukhopadhyay M. Natural Extracts Using Supercritical Carbon Dioxide; CRC Press, 2000
2) Somogyi L. "The flavour and fragrance industry: serving a global market" Chemistry and Industry 1996, 5, 170-3
3) Extraction of Natural Products Using Near Critical Solvents, King M.B., Bott T.R. Eds; Chapman & Hall, 1993
4) Chan K. "Some aspects of toxic contaminants in herbal medicine" Chemosphere 2003, 52, 1361
5) Beckman E.J. "Supercritical and near critical CO2 in green chemical synthesis and processing" J. Supercritical Fluids 2004, 28 (2-3), 121-91
6) Mohamed R.S., MANSOORI G.A. "The Use of Supercritical Fluid Extraction Technology in Food Processing" Food Technology Magazine 2002, June
7) Del Valle J.M., AGUILERA J.M. Food Science and Technology International 1999, 5, 1-24
8) De Castro M.D.L., JIMENEZ-CARMONA M.M. "High pressure CO2 extraction: fundamentals and applications in the food industry" Trac- Trends in Analytical Chemistry 2000, 19, 223-8
10) Di Giacomo G., et al. "Solubility of essential oils component in compressed SC-CO2" Fluid Phase Equil. 1989, 52, 405-11
Worldwide pharmaceutical industry launches global health progress initiative to expand efforts to improve health in developing countries industry supports hundreds of programs helping millions in the developing world and is looking for new partners
The worldwide pharmaceutical industry launched Global Health Progress, an initiative to bring research-based biopharmaceutical companies, global health leaders and policymakers together to build on current partnerships to improve health in the developing world.
Serving as a convening point for the industry and its partners, Global Health Progress will facilitate interaction between the private sector, NGOs and governments to share research and best practices; raise awareness of global health challenges; and build partnerships to improve global health. “Research-based biopharmaceutical companies contribute hugely to health partnerships for the developing world, through their unique expertise in R&D, regulatory affairs, manufacturing, logistics and many other fields, but we can’t work alone.“ said Dr. HARVEY BALE, Director General of IFPMA. “The Global Health Progress initiative should help to expand the range and scope of global health partnerships supported by our industry.” Global Health Progress unveiled its web site, www.globalhealthprogress.org, which houses a database of research-based biopharmaceutical companies’ global health programs, including information on more than 300 partners, 400 programs and ongoing investments of billions of dollars annually in products and man-hours. Featuring stories of health workers on the ground, the site highlights organizations and individuals who are making a difference in global health.
Important new discoveries from nms on CDC7 inhibitor, a protein responsible for the proliferation of tumour cells
Scientists from Nerviano Medical Sciences (NMS), one of the largest stand alone Research and Development facility for anticancer drugs in Europe, have discovered and developed a new molecule that is active against tumour cells. Oncological research is focusing more and more on targeted therapies for cancer and the NMS’ molecule is a low molecular weight inhibitor of Cdc7, a kinase previously identified by NMS’ scientists as being responsible for the uncontrolled proliferation of tumours. This discovery was presented and discussed at the Annual Meeting of the American Association for Cancer Research held in San Diego. The AACR is the most important international congress for the presentation of new knowledge and new experimental cancer drugs.
The pre-clinical results generated by NMS’ scientists indicate that this Cdc7 inhibitor blocks uncontrolled proliferation of cancer cells and induces cell death by apoptosis. The compound is efficacious on cancers cells of various origins, including those resistant to the tumour replication inhibitors already on the market. The clinical trials for the Cdc7 inhibitor will start in the next few months in a variety of human tumours, including ovary, colon and breast cancers along with various forms of leukaemia.